прием ПЭТ-бутылок. Как выбрать и где установить автомат по сбору пластиковых бутылок? :: BusinessMan.ru
Пластик является одним из главных врагов для всего живого. Именно поэтому уже не один десяток лет человечество ведет борьбу с упаковками и бутылками, которые загрязняют окружающую среду. По результатам исследований, проведенных учеными, был сделан однозначный вывод о том, что разложение пластика происходит около двухсот лет.
На протяжении этого периода данные отходы отравляют ту территорию, на которой располагаются. Стоит сказать, что с каждым годом производство пластиковой упаковки во всем мире увеличивается стремительными темпами. Это является основной причиной роста количества отходов из данного материала.
Решение экологической проблемы
На сегодняшний день для того, чтобы остановить загрязнение планеты пластиком, необходимо полностью отказаться от его производства. Однако данный вариант является нереальным. Дело в том, что пластик — универсальный и дешевый материал, который применяется практически во всех сферах деятельности человека. К тому же на данный момент достойной альтернативы ему не существует.
Сокращению количества вредных отходов может посодействовать ограничение производства экологически небезопасных упаковок. Этот метод в настоящее время используется во многих зарубежных странах. Например, в магазинах Европы полиэтиленовые пакеты заменили бумажными, которые не вредят экологии и способны при утилизации разложиться за две-четыре недели.
Сокращение количества отходов из пластика может быть достигнуто и при вторичной переработке этого материала. Основной объем упаковок, подлежащих утилизации, приходится на бутылки. Практически все производители газированных и минеральных вод разливают их в пластиковые бутылки. В связи с этим и возникает проблема утилизации. Решая ее, можно открыть собственный бизнес на пластиковых бутылках.
Сбор отходов
Прежде чем организовать прием ПЭТ-бутылок, следует внимательно изучить опыт европейских бизнесменов. На территории торговых точек большинства стран устанавливаются специальные автоматы. Основным их предназначением является сбор ПЭТ-бутылок. Если внимательно изучить этот вопрос, то можно сделать вывод о том, что заработать на таких отходах можно. Однако сделать это непросто. В настоящий момент в России прием ПЭТ-бутылок осуществляет одна-единственная компания, которой оказывает помощь московское правительство.
Разновидности автоматов
Устройство, при помощи которого может быть осуществлен прием ПЭТ-бутылок, представляет собой специальный контейнер для тары. При этом для определения объекта производится его сканирование. В мировой практике существует две разновидности подобных автоматов. К первой из них относят такие, которые осуществляют сканирование и прием ПЭТ-бутылок. Вторая разновидность автоматов создана для сбора алюминиевой тары.
Принцип действия
«Умные» контейнеры называются фандоматами. Автоматы по сбору пластиковых бутылок и алюминиевой тары обменивают подлежащую утилизации упаковку на деньги. В этих контейнерах производится определение объема и веса тары, а также распознаются штрих-коды, позволяющие идентифицировать объект.
Автомат по сбору пластиковых бутылок и алюминиевой тары оснащен системой «микроклимат», которая поддерживает определенные значения влажности и температуры и позволяет устройству работать бесперебойно.
Приобретение
Производство таких машин налажено в Германии. В связи с этим цена данного оборудования немалая. Стоимостный диапазон фандоматов находится в пределах от четырех тысяч восьмисот до семи тысяч евро.
Покупать или нет такой автомат? Начиная свое дело, каждый предприниматель делает выводы о сроках окупаемости приобретаемого им оборудования. Сбор пластиковых бутылок как бизнес – занятие не из легких. Именно поэтому перед тем как предпринимать определенные шаги, необходимо заручиться поддержкой государственных органов.
Вендинговый бизнес продвинется быстрее и принесет реальную прибыль в том случае, когда сбор пластмассовой тары будет объединен с ее переработкой. Два этих процесса практически неотделимы друг от друга. Для того чтобы сырье переработать, его, прежде всего, необходимо собрать. При этом лучшим местом для размещения фандоматов будут служить торговые залы магазинов или территория перед входом в супер- и минимаркеты.
Рентабельность бизнеса
Предположим, что в городе установлено две тысячи фандоматов. Наиболее выгодно принимать алюминиевую тару. Контейнер по ее сбору может вместить до четырехсот банок. Следовательно, со всех фандоматов ежедневное поступление составит 800 000 банок.
Стоимость алюминиевого сырья (1,28 доллара за килограмм) позволит получить дневную выручку в размере 25,5 тыс. долларов. Из них аппаратом будет выплачено тем, кто опустил в него банки, 18,5 тыс. дол. В итоге ежедневная прибыль составит семь тысяч долларов. Но не стоит забывать о том, что на покупку такого количества фандоматов уйдет двенадцать миллионов евро.
Таким образом, при благоприятных условиях получение прибыли возможно только спустя пять-шесть лет после начала бизнеса. При этом мы не включили в свой расчет расходы на администрирование, логистику и техническую поддержку. Вывод однозначен. Для того чтобы построить сеть фандоматов, потребуется помощь государства.
Сбор и переработка
Статистические данные мировой практики свидетельствуют о том, что упаковка и прием тары – это самые невыгодные звенья цепочки переработки пластика. Такое положение дел существует практически во всех странах. Для бизнеса необходимым условием является дотация бюджета и поддержка властей города.
Большей доходностью обладает следующий этап – переработка пластика. Существует определенное мнение экспертов. Согласно ему, окупаемость предприятия по переработке мусора достигается в течение одного-двух лет с момента его открытия.
При этом в среднем показатели рентабельности достигают двадцати пяти процентов. Более высокий доход может быть получен при объединении двух процессов – сбора и переработки пластиковой тары. Однако для открытия такого бизнеса непременно понадобятся дотации государства.
Кроме того, некоторые эксперты полагают, что фандоматы в России в настоящее время осуществляют неверную схему вознаграждения. Так, в Германии человеку, бросившему в устройство бутылку или банку, выдается специальный талон, который позволяет снизить стоимость приобретенных в магазине продуктов. В нашей стране человеку проще выбросить в урну пустую бутылку, чем проделать путь к фандомату, который выдаст ему в обмен на тару какую-то мелочь.
Некоторые эксперты полагают, что привлечь внимание к устройству по сбору пластиковых бутылок можно и другим способом. Если фандомат в обмен на тару исполнит музыкальную композицию или «расскажет» шутку, то люди будут прогуливаться не к урне, а к нему. При этом можно достичь значительной экономии денежных средств на выдачу.
Использование отработанного пластика
Несмотря на трудности бизнеса по приему ПЭТ-бутылок, в России планируется расширение сети фандоматов. Как используется отработанный пластик?
На эти цели уходит практически тридцать процентов отходов. Волокна из ПЭТ используются для обивки автомобилей. Из них изготавливают ковровые покрытия для офисов и домов. ПЭТ европейского стандарта находит свое применение при производстве полотна полиэстера. Этот материал применяется в качестве утеплителя для спальных мешков и спортивной одежды, а также как наполнитель для мягких игрушек. Если волокно тонкое, то оно используется при производстве искусственной шерсти для шарфов, свитеров и трикотажных рубашек.
Вывод
Создание бизнеса по сбору и переработке ПЭТ-бутылок и алюминиевой тары потребует много усилий и времени. При этом немаловажна поддержка государства. Однако, преодолев все препятствия, вы сможете придти к небывалому результату, и тогда все затраты будут перекрыты доходом. Самое главное – верить в успех, и тогда все непременно получится.
businessman.ru
Как перерабатывают пластиковые бутылки — Как это сделано, как это работает, как это устроено

Фото: © Гринпис / Игорь Подгорный
Большинство из нас покупает напитки в пластиковых бутылках. Кто-то чаще, кто-то реже. Но мало кто сдает эти бутылки в специальные пункты приема. А некоторые люди, в том числе чиновники, занимающиеся проблемой отходов, уверены, что переработка подобного сырья в России — дело далекого будущего.
А между тем, совсем недалеко от Москвы, рядом с городом Солнечногорск с 2007 года работает завод по переработке пластмасс «Пларус» — первое российское предприятие, использующее уникальную технологию переработки пластиковой упаковки «бутылка в бутылку» (bottle-to-bottle).
Рекламная перетяжка в Солнечногорске, призывающая выбрасывать пластик только в специальные контейнеры.
Один из таких контейнеров установлен у лицея №8. Еще около 70 таких сеток установлены по всему Солнечногорску в рамках проекта по раздельному сбору и переработке пластиковых бутылок, который стартовал в сентябре 2011 г. Инициаторы проекта — Администрация Солнечногорского муниципального района, завод «Пларус», компания «Кока-Кола» и крупнейшей производитель безалкогольных напитков Coca-Cola Hellenic в России.
Но, несмотря на то, что в рамках проекта проводятся образовательные мероприятия, людям объясняют важность раздельного сбора, не все жители Солнечногорска разделяют благие идеи.
Пока мы снимали контейнер у лицея, один из проходивших родителей поинтересовался: ну что, мужики, заканчиваете наконец-то эксперимент? На наш вопрос о том, как он относится к тому, что пластик собирают и отправляют на переработку, мужчина сказал: ну…им-то (переработчикам) хорошо, а нам этим дышать.
Парадоксально, но многие жители Солнечногорска и окрестностей уверены, что «Пларус» их травит. Конечно, мы поинтересовались у руководства завода, откуда взялось это убеждение и как у них обстоят дела с выбросами вредных веществ. Оказалось, что на месте, где сейчас стоит «Пларус», некоторое время назад действительно собирались построить какое-то химическое предприятие. Вот люди и запомнили это и теперь переносят свои тревогу на предприятие, которое при всем желании не может производить те «ужасные запахи» и «ядовитый дым», которые чудятся солнечногорцам. Кроме того, время от времени на завод приезжают комиссии, которые проверяют производство, реагируя на обращения местных жителей. До сих пор, претензий к заводу не было.
Бутылки из сеток-контейнеров грузят в машину и отвозят на завод. На предприятии собираются в скором времени приобрести мини-пресс, чтобы возить меньше воздуха, а больше собранных по городу бутылок.
Знакомство с заводом мы начали с разговора с коммерческим директором Николаем Владиславовичем Шведом. Он рассказал о работе завода, о «подводных камнях», которые пришлось преодолеть, налаживая эффективное производство. Сейчас основные проблемы — дефицит сырья и недостаточная поддержка со стороны властей. Если администрация Солнечногорского района приняла участие в организации точек сбора пластика, власти ближайшего Зеленограда (не говоря уже о Москве) пока не торопятся перенимать положительный опыт.
Это — конечный продукт «Пларуса» — гранулы, из которых делают бутылки.
В зависимости от исходного сырья гранулы получаются разного цвета и качества.
А это преформы, которые производят из гранул. Из преформ и «выдувают» те самые, привычные нам бутылки для напитков и технических жидкостей.
А это — сырье, собранные ПЭТ-бутылки.
К сожалению, не все собранные бутылки одинаково хороши для переработки. На этом снимке видны красные бутылки из-под пива. Кому-то показалось, что это удачный маркетинговый ход. Но, скорей всего, они не пойдут на переработку. Слишком большая плотность, слишком много красителя.
Разгрузка очередной фуры с бутылками.
И вот мы в первом цеху.
Здесь кипы с пластиком складируют и сортируют.
На ленту транспортера вываливают все, что есть в кипах и отправляют на первичную сортировку.
Увы, в кипах приезжает не только пластик. Вот список того, что не подлежит переработке на этом заводе.
Все это мы вытащили прямо с ленты транспортера.
Бутылки из-под бытовой химии, подсолнечного масла, кефира, подложки от тортиков, бумага — все это не нужно класть в контейнеры для сбора пластика. В идеале, конечно, вообще не покупать товары в подобной упаковке, но, к сожалению, это возможно не всегда.
Кипы с пластиковыми бутылками весьма фотогеничны ))
Этих пластиковых курганов, которые приходится развозить в ковшах, здесь совсем скоро не останется. Как только на заводе отремонтируют пресс, все сырье будет храниться в кипах. С кипами и работать удобнее, и места они занимают гораздо меньше.
Досортировывать сырье приходится вручную. От этого этапа напрямую зависит качество готовой продукции.
После сортировки бутылки отправляются в специальные агрегаты, где их разделяют по основным цветам.
Это цех мойки. Бутылки нужно отмыть от грязи и этикеток.
К сожалению, в России, в отличии, скажем, от Белоруссии, нет стандартов на клей, которым этикетки приклеивают к бутылкам. Поэтому от некоторых бутылок они не отмываются даже в специальном щелочном растворе. Так что, если вы сдаете бутылку на переработку, этикетку (особенно термоусадочную) лучше все-таки срезать. Отмытые этикетки (и крышечки от бутылок), кстати, тоже идут в дело.
После того, как бутылки отмыты, они идут «под нож». Полученный материал разделяют по цветам с помощью специальной машины. Пыль от резки ПЭТ отделяют в специальных колоннах, на фильтрах с помощью противотока воздуха.
Вот этот промежуточный результат работы — флекс. Из него и делают гранулы. Разноцветный флекс служит сырьем для производств, где изделия красят и где нет особых требований к чистоте сырья. Из такого вот флекса можно делать, например, пластмассовые тазики )) Да, исходником для этих разноцветных хлопьев являются пробки от бутылок!
Отсюда контролируют технологический процесс.
Здесь же, под мощной лупой каждые 15 минут визуально проверяют качество готовых гранул. Их цвет должен быть равномерным, в гранулах не должно быть каких-либо включений.
Ну а это финальный этап производства. На фото — экструдер — агрегат, где при температуре около 280С флекс превращается в будущие гранулы.
Из экструдера вылезают вот такие макаронины.
Их охлаждают водой и режут на гранулы.
Завораживающее зрелище )
Склад готовой продукции. В каждом таком мешке — 1 тонна, плюс/минус 50 кг.
На прощанье залезаем на галерею, чтобы посмотреть на производство сверху. Здесь довольно тепло и влажно, объектив сразу запотевает, как в бане ))
Сейчас на «Пларусе» делают сырье, пригодное для производства только технических бутылок. Но совсем скоро на предприятии по результатам экспертизы качества сырья (а оно весьма высоко), должны получить сертификат, который позволит использовать гранулы «Пларуса» для производства бутылки, годной для пищевой промышленности!
Будем рады вопросам, комментариям и, конечно, перепостам. Глядишь, и «сильные мира сего» наконец заметят, что у них под боком работает завод, который готов помочь в решении проблемы отходов.
Все фото: © Гринпис / Игорь Подгорный
kak-eto-sdelano.livejournal.com
Вторая жизнь пластиковой бутылки: gp_russia — LiveJournal
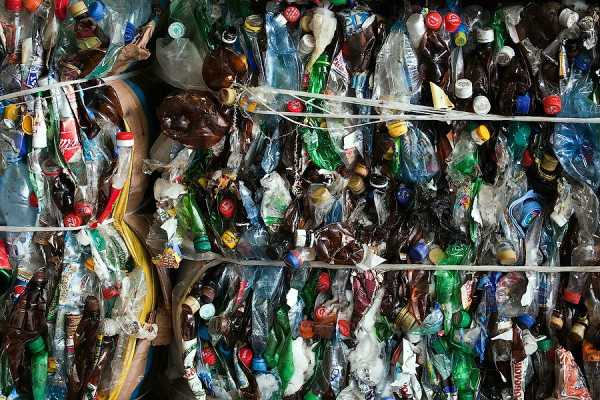
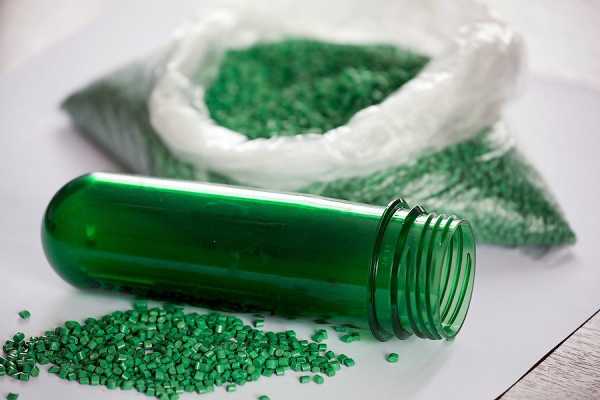
Фото: © Гринпис / Игорь Подгорный
Большинство из нас покупает напитки в пластиковых бутылках. Кто-то чаще, кто-то реже. Но мало кто сдает эти бутылки в специальные пункты приема. А некоторые люди, в том числе чиновники, занимающиеся проблемой отходов, уверены, что переработка подобного сырья в России — дело далекого будущего.
А между тем, совсем недалеко от Москвы, рядом с городом Солнечногорск с 2007 года работает завод по переработке пластмасс «Пларус» — первое российское предприятие, использующее уникальную технологию переработки пластиковой упаковки «бутылка в бутылку» (bottle-to-bottle).
Рекламная перетяжка в Солнечногорске, призывающая выбрасывать пластик только в специальные контейнеры.
Один из таких контейнеров установлен у лицея №8. Еще около 70 таких сеток установлены по всему Солнечногорску в рамках проекта по раздельному сбору и переработке пластиковых бутылок, который стартовал в сентябре 2011 г. Инициаторы проекта — Администрация Солнечногорского муниципального района, завод «Пларус», компания «Кока-Кола» и крупнейшей производитель безалкогольных напитков Coca-Cola Hellenic в России.
Но, несмотря на то, что в рамках проекта проводятся образовательные мероприятия, людям объясняют важность раздельного сбора, не все жители Солнечногорска разделяют благие идеи.
Пока мы снимали контейнер у лицея, один из проходивших родителей поинтересовался: ну что, мужики, заканчиваете наконец-то эксперимент? На наш вопрос о том, как он относится к тому, что пластик собирают и отправляют на переработку, мужчина сказал: ну…им-то (переработчикам) хорошо, а нам этим дышать.
Парадоксально, но многие жители Солнечногорска и окрестностей уверены, что «Пларус» их травит. Конечно, мы поинтересовались у руководства завода, откуда взялось это убеждение и как у них обстоят дела с выбросами вредных веществ. Оказалось, что на месте, где сейчас стоит «Пларус», некоторое время назад действительно собирались построить какое-то химическое предприятие. Вот люди и запомнили это и теперь переносят свои тревогу на предприятие, которое при всем желании не может производить те «ужасные запахи» и «ядовитый дым», которые чудятся солнечногорцам. Кроме того, время от времени на завод приезжают комиссии, которые проверяют производство, реагируя на обращения местных жителей. До сих пор, претензий к заводу не было.
Бутылки из сеток-контейнеров грузят в машину и отвозят на завод. На предприятии собираются в скором времени приобрести мини-пресс, чтобы возить меньше воздуха, а больше собранных по городу бутылок.
Знакомство с заводом мы начали с разговора с коммерческим директором Николаем Владиславовичем Шведом. Он рассказал о работе завода, о «подводных камнях», которые пришлось преодолеть, налаживая эффективное производство. Сейчас основные проблемы — дефицит сырья и недостаточная поддержка со стороны властей. Если администрация Солнечногорского района приняла участие в организации точек сбора пластика, власти ближайшего Зеленограда (не говоря уже о Москве) пока не торопятся перенимать положительный опыт.
Это — конечный продукт «Пларуса» — гранулы, из которых делают бутылки.
В зависимости от исходного сырья гранулы получаются разного цвета и качества.
А это преформы, которые производят из гранул. Из преформ и «выдувают» те самые, привычные нам бутылки для напитков и технических жидкостей.
А это — сырье, собранные ПЭТ-бутылки.
К сожалению, не все собранные бутылки одинаково хороши для переработки. На этом снимке видны красные бутылки из-под пива. Кому-то показалось, что это удачный маркетинговый ход. Но, скорей всего, они не пойдут на переработку. Слишком большая плотность, слишком много красителя.
Разгрузка очередной фуры с бутылками.
И вот мы в первом цеху.
Здесь кипы с пластиком складируют и сортируют.
На ленту транспортера вываливают все, что есть в кипах и отправляют на первичную сортировку.
Увы, в кипах приезжает не только пластик. Вот список того, что не подлежит переработке на этом заводе.
Все это мы вытащили прямо с ленты транспортера.
Бутылки из-под бытовой химии, подсолнечного масла, кефира, подложки от тортиков, бумага — все это не нужно класть в контейнеры для сбора пластика. В идеале, конечно, вообще не покупать товары в подобной упаковке, но, к сожалению, это возможно не всегда.
Кипы с пластиковыми бутылками весьма фотогеничны ))
Этих пластиковых курганов, которые приходится развозить в ковшах, здесь совсем скоро не останется. Как только на заводе отремонтируют пресс, все сырье будет храниться в кипах. С кипами и работать удобнее, и места они занимают гораздо меньше.
Досортировывать сырье приходится вручную. От этого этапа напрямую зависит качество готовой продукции.
После сортировки бутылки отправляются в специальные агрегаты, где их разделяют по основным цветам.
Это цех мойки. Бутылки нужно отмыть от грязи и этикеток.
К сожалению, в России, в отличии, скажем, от Белоруссии, нет стандартов на клей, которым этикетки приклеивают к бутылкам. Поэтому от некоторых бутылок они не отмываются даже в специальном щелочном растворе. Так что, если вы сдаете бутылку на переработку, этикетку (особенно термоусадочную) лучше все-таки срезать. Отмытые этикетки (и крышечки от бутылок), кстати, тоже идут в дело.
После того, как бутылки отмыты, они идут «под нож». Полученный материал разделяют по цветам с помощью специальной машины. Пыль от резки ПЭТ отделяют в специальных колоннах, на фильтрах с помощью противотока воздуха.
Вот этот промежуточный результат работы — флекс. Из него и делают гранулы. Разноцветный флекс служит сырьем для производств, где изделия красят и где нет особых требований к чистоте сырья. Из такого вот флекса можно делать, например, пластмассовые тазики )) Да, исходником для этих разноцветных хлопьев являются пробки от бутылок!
Отсюда контролируют технологический процесс.
Здесь же, под мощной лупой каждые 15 минут визуально проверяют качество готовых гранул. Их цвет должен быть равномерным, в гранулах не должно быть каких-либо включений.
Ну а это финальный этап производства. На фото — экструдер — агрегат, где при температуре около 280С флекс превращается в будущие гранулы.
Из экструдера вылезают вот такие макаронины.
Их охлаждают водой и режут на гранулы.
Завораживающее зрелище )
Склад готовой продукции. В каждом таком мешке — 1 тонна, плюс/минус 50 кг.
На прощанье залезаем на галерею, чтобы посмотреть на производство сверху. Здесь довольно тепло и влажно, объектив сразу запотевает, как в бане ))
Сейчас на «Пларусе» делают сырье, пригодное для производства только технических бутылок. Но совсем скоро на предприятии по результатам экспертизы качества сырья (а оно весьма высоко), должны получить сертификат, который позволит использовать гранулы «Пларуса» для производства бутылки, годной для пищевой промышленности!
Будем рады вопросам, комментариям и, конечно, перепостам. Глядишь, и «сильные мира сего» наконец заметят, что у них под боком работает завод, который готов помочь в решении проблемы отходов.
Напоминаем, что еще не поздно принять участие в конкурсе и выиграть флисовую куртку с логотипом Гринпис, сделанную из таких же гранул, как производят на «Пларусе»: http://www.votegreenpeace.ru/winflis/
Все фото: © Гринпис / Игорь Подгорный
P.S. Материалы по теме:
Вторая жизнь стеклянной бутылки: http://gp-russia.livejournal.com/1560864.html
Вторая жизнь вещей предприятие «Петромакс», перерабатывающая бытовую технику и электронику: http://gp-russia.livejournal.com/1502236.html
Опыт раздельного сбора отходов в торговых сетях Волгограда: http://gp-russia.livejournal.com/1668124.html
gp-russia.livejournal.com
Вторая жизнь пластиковой бутылки: igorpodgorny — LiveJournal
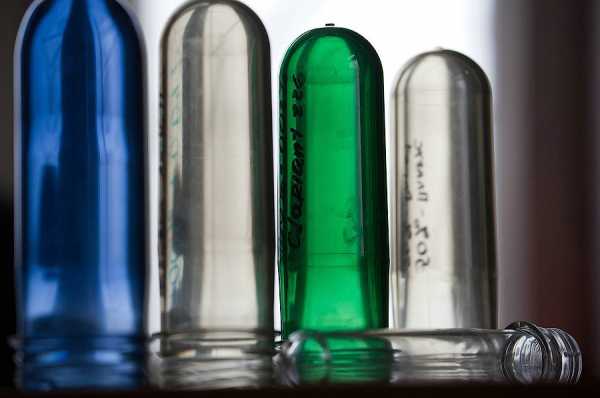
Фото: © Гринпис / Игорь Подгорный
Большинство из нас покупает напитки в пластиковых бутылках. Кто-то чаще, кто-то реже. Но мало кто сдает эти бутылки в специальные пункты приема. А некоторые люди, в том числе чиновники, занимающиеся проблемой отходов, уверены, что переработка подобного сырья в России — дело далекого будущего.
А между тем, совсем недалеко от Москвы, рядом с городом Солнечногорск с 2007 года работает завод по переработке пластмасс «Пларус» — первое российское предприятие, использующее уникальную технологию переработки пластиковой упаковки «бутылка в бутылку» (bottle-to-bottle).
Рекламная перетяжка в Солнечногорске, призывающая выбрасывать пластик только в специальные контейнеры.
Один из таких контейнеров установлен у лицея №8. Еще около 70 таких сеток установлены по всему Солнечногорску в рамках проекта по раздельному сбору и переработке пластиковых бутылок, который стартовал в сентябре 2011 г. Инициаторы проекта — Администрация Солнечногорского муниципального района, завод «Пларус», компания «Кока-Кола» и крупнейшей производитель безалкогольных напитков Coca-Cola Hellenic в России.
Но, несмотря на то, что в рамках проекта проводятся образовательные мероприятия, людям объясняют важность раздельного сбора, не все жители Солнечногорска разделяют благие идеи.
Пока мы снимали контейнер у лицея, один из проходивших родителей поинтересовался: ну что, мужики, заканчиваете наконец-то эксперимент? На наш вопрос о том, как он относится к тому, что пластик собирают и отправляют на переработку, мужчина сказал: ну…им-то (переработчикам) хорошо, а нам этим дышать.
Парадоксально, но многие жители Солнечногорска и окрестностей уверены, что «Пларус» их травит. Конечно, мы поинтересовались у руководства завода, откуда взялось это убеждение и как у них обстоят дела с выбросами вредных веществ. Оказалось, что на месте, где сейчас стоит «Пларус», некоторое время назад действительно собирались построить какое-то химическое предприятие. Вот люди и запомнили это и теперь переносят свои тревогу на предприятие, которое при всем желании не может производить те «ужасные запахи» и «ядовитый дым», которые чудятся солнечногорцам. Кроме того, время от времени на завод приезжают комиссии, которые проверяют производство, реагируя на обращения местных жителей. До сих пор, претензий к заводу не было.
Бутылки из сеток-контейнеров грузят в машину и отвозят на завод. На предприятии собираются в скором времени приобрести мини-пресс, чтобы возить меньше воздуха, а больше собранных по городу бутылок.
Знакомство с заводом мы начали с разговора с коммерческим директором Николаем Владиславовичем Шведом. Он рассказал о работе завода, о «подводных камнях», которые пришлось преодолеть, налаживая эффективное производство. Сейчас основные проблемы — дефицит сырья и недостаточная поддержка со стороны властей. Если администрация Солнечногорского района приняла участие в организации точек сбора пластика, власти ближайшего Зеленограда (не говоря уже о Москве) пока не торопятся перенимать положительный опыт.
Это — конечный продукт «Пларуса» — гранулы, из которых делают бутылки.
В зависимости от исходного сырья гранулы получаются разного цвета и качества.
А это преформы, которые производят из гранул. Из преформ и «выдувают» те самые, привычные нам бутылки для напитков и технических жидкостей.
А это — сырье, собранные ПЭТ-бутылки.
К сожалению, не все собранные бутылки одинаково хороши для переработки. На этом снимке видны красные бутылки из-под пива. Кому-то показалось, что это удачный маркетинговый ход. Но, скорей всего, они не пойдут на переработку. Слишком большая плотность, слишком много красителя.
Разгрузка очередной фуры с бутылками.
И вот мы в первом цеху.
Здесь кипы с пластиком складируют и сортируют.
На ленту транспортера вываливают все, что есть в кипах и отправляют на первичную сортировку.
Увы, в кипах приезжает не только пластик. Вот список того, что не подлежит переработке на этом заводе.
Все это мы вытащили прямо с ленты транспортера.
Бутылки из-под бытовой химии, подсолнечного масла, кефира, подложки от тортиков, бумага — все это не нужно класть в контейнеры для сбора пластика. В идеале, конечно, вообще не покупать товары в подобной упаковке, но, к сожалению, это возможно не всегда.
Кипы с пластиковыми бутылками весьма фотогеничны ))
Этих пластиковых курганов, которые приходится развозить в ковшах, здесь совсем скоро не останется. Как только на заводе отремонтируют пресс, все сырье будет храниться в кипах. С кипами и работать удобнее, и места они занимают гораздо меньше.
Досортировывать сырье приходится вручную. От этого этапа напрямую зависит качество готовой продукции.
После сортировки бутылки отправляются в специальные агрегаты, где их разделяют по основным цветам.
Это цех мойки. Бутылки нужно отмыть от грязи и этикеток.
К сожалению, в России, в отличии, скажем, от Белоруссии, нет стандартов на клей, которым этикетки приклеивают к бутылкам. Поэтому от некоторых бутылок они не отмываются даже в специальном щелочном растворе. Так что, если вы сдаете бутылку на переработку, этикетку (особенно термоусадочную) лучше все-таки срезать. Отмытые этикетки (и крышечки от бутылок), кстати, тоже идут в дело.
После того, как бутылки отмыты, они идут «под нож». Полученный материал разделяют по цветам с помощью специальной машины. Пыль от резки ПЭТ отделяют в специальных колоннах, на фильтрах с помощью противотока воздуха.
Вот этот промежуточный результат работы — флекс. Из него и делают гранулы. Разноцветный флекс служит сырьем для производств, где изделия красят и где нет особых требований к чистоте сырья. Из такого вот флекса можно делать, например, пластмассовые тазики )) Да, исходником для этих разноцветных хлопьев являются пробки от бутылок!
Отсюда контролируют технологический процесс.
Здесь же, под мощной лупой каждые 15 минут визуально проверяют качество готовых гранул. Их цвет должен быть равномерным, в гранулах не должно быть каких-либо включений.
Ну а это финальный этап производства. На фото — экструдер — агрегат, где при температуре около 280С флекс превращается в будущие гранулы.
Из экструдера вылезают вот такие макаронины.
Их охлаждают водой и режут на гранулы.
Завораживающее зрелище )
Склад готовой продукции. В каждом таком мешке — 1 тонна, плюс/минус 50 кг.
На прощанье залезаем на галерею, чтобы посмотреть на производство сверху. Здесь довольно тепло и влажно, объектив сразу запотевает, как в бане ))
Сейчас на «Пларусе» делают сырье, пригодное для производства только технических бутылок. Но совсем скоро на предприятии по результатам экспертизы качества сырья (а оно весьма высоко), должны получить сертификат, который позволит использовать гранулы «Пларуса» для производства бутылки, годной для пищевой промышленности!
Будем рады вопросам, комментариям и, конечно, перепостам. Глядишь, и «сильные мира сего» наконец заметят, что у них под боком работает завод, который готов помочь в решении проблемы отходов.
Напоминаем, что еще не поздно принять участие в конкурсе и выиграть флисовую куртку с логотипом Гринпис, сделанную из таких же гранул, как производят на «Пларусе»: http://www.votegreenpeace.ru/winflis/
Все фото: © Гринпис / Игорь Подгорный
P.S. Материалы по теме:
Вторая жизнь стеклянной бутылки: http://gp-russia.livejournal.com/1560864.html
Вторая жизнь вещей предприятие «Петромакс», перерабатывающая бытовую технику и электронику: http://igorpodgorny.livejournal.com/312276.html
Опыт раздельного сбора отходов в торговых сетях Волгограда: http://gp-russia.livejournal.com/1668124.html
igorpodgorny.livejournal.com
Тайная жизнь пластиковой бутылки | Greenpeace в России
Сегодня у пластиковой бутылки есть два способа покончить с жизнью: сотни лет гнить на свалке или оказаться в переработке и стать новой нужной вещью. Мы решили рассказать вам подробнее о втором способе. Но сначала немного фактов.
Сегодня в России нет полноценной системы переработки отходов. То есть наши бутылки, консервные банки, яблочные огрызки и прочие отходы лишены права стать после смерти чем-то полезным в отличие, между прочим, от отходов других стран. Чуть больше месяца назад Гринпис запустил проект «Миллион за раздельный сбор» , в рамках которого жители нашей страны могут направить письма своим мэру и губернатору и потребовать раздельный сбор отходов. Уже более 40000 человек поддержали нас, происходят первые встречи экспертов Гринпис с региональными властями.
Однако благодаря письмам и отзывам наших сторонников, мы поняли, что многие жители нашей страны опасаются, что раздельно собранные отходы поедут на свалку, поскольку в России нет ни одного предприятия по переработке отходов. Мы решили рассказать, что это не так. Сегодня в России уже действуют сотни предприятий в разных регионах. Вот репортаж с одного из них.
Перерождение пластиковой бутылки
С 2007 года совсем недалеко от Москвы, рядом с городом Солнечногорск, работает завод по переработке пластмасс «Пларус» — первое российское предприятие, использующее уникальную технологию переработки пластиковой упаковки «бутылка в бутылку» (bottle-to-bottle).
Инициаторы проекта — Администрация Солнечногорского муниципального района, завод «Пларус», компания «Кока-Кола» и крупнейшей производитель безалкогольных напитков Coca-Cola Hellenic в России. Мы встречались с коммерческим директором «Пларус» Николаем Владиславовичем Шведом в 2012 году. Ещё тогда он называл основными проблемами — дефицит сырья и недостаточную поддержку со стороны властей. Если администрация Солнечногорского района приняла участие в организации точек сбора пластика, власти ближайшего Зеленограда (не говоря уже о Москве) не торопились перенимать положительный опыт.
Несмотря на это завод продолжает развиваться. Конечный продукт «Пларуса» — гранулы, из которых делают бутылки. В зависимости от исходного сырья гранулы получаются разного цвета и качества.
А это преформы, которые производят из гранул. Из преформ и «выдувают» те самые, привычные нам бутылки для напитков и технических жидкостей. Если раньше на заводе производили только технические бутылки, то теперь делают и бутылки пищевого назначения.
А это — сырьё, собранные ПЭТ-бутылки. К сожалению, не все собранные бутылки одинаково хороши для переработки. На этом снимке видны красные бутылки из-под пива. Кому-то показалось, что это удачный маркетинговый ход. Но, скорей всего, они не пойдут на переработку. Слишком большая плотность, слишком много красителя.
И вот мы в первом цеху. Здесь кипы с пластиком складируют и сортируют. На ленту транспортера вываливают всё, что есть в кипах и отправляют на первичную сортировку.
Досортировывать сырьё приходится вручную. От этого этапа напрямую зависит качество готовой продукции. После сортировки бутылки отправляются в специальные агрегаты, где их разделяют по основным цветам.
Это цех мойки. Бутылки нужно отмыть от грязи и этикеток.
К сожалению, в России, в отличие, скажем, от Белоруссии, нет стандартов на клей, которым этикетки приклеивают к бутылкам. Поэтому от некоторых бутылок они не отмываются даже в специальном щелочном растворе. Так что, если вы сдаёте бутылку на переработку, этикетку (особенно термоусадочную) лучше всё-таки срезать. Отмытые этикетки (и крышечки от бутылок), кстати, тоже идут в дело. После того, как бутылки отмыты, они идут «под нож». Полученный материал разделяют по цветам с помощью специальной машины. Пыль от резки ПЭТ отделяют в специальных колоннах, на фильтрах с помощью противотока воздуха.
Вот этот промежуточный результат работы — флекс. Из него и делают гранулы. Разноцветный флекс служит сырьем для производств, где изделия красят и где нет особых требований к чистоте сырья. Из такого вот флекса можно делать, например, пластмассовые тазики, флисовые кофты. Да, исходником для этих разноцветных хлопьев являются пробки от бутылок!
В отдельной комнате контролируют технологический процесс. Здесь же, под мощной лупой каждые 15 минут визуально проверяют качество готовых гранул. Их цвет должен быть равномерным, в гранулах не должно быть каких-либо включений.
Ну а это финальный этап производства. На фото — экструдер — агрегат, где при температуре около 280С флекс превращается в будущие гранулы.
Из экструдера вылезают вот такие макаронины.Их охлаждают водой и режут на гранулы.
Такая вторая жизнь может быть у каждой пластиковой бутылки, для этого только нужно заставить свои региональные власти наладить систему раздельного сбора. Направьте письма вашим мэру и губернатору прямо сейчас. Для это нужно кликнуть эту страницу.
www.greenpeace.org
Как перерабатывают пластиковые бутылки — Как это сделано, как это работает, как это устроено
«Изготовлено из переработанного пластика». Такие надписи встречаются на самых различных изделиях — канистрах, расческах, даже детских игрушках. В цивилизованном мире технологии переработки пластика уже шагнули далеко — и позволяют перерабатывать пластиковые бутылки ПЭТ не только в тазики, но и … в точно такие же пластиковые бутылки. На сегодняшний день в России существует всего один завод, работающий по технологии bottle-to-bottle. Давайте посмотрим, как устроено это производство.
Завод «Пларус» был открыт в 2007 году на окраине подмосковного Солнечногорска.
Сегодня тут перерабатывают 1800-2500 тонн пластиковых бутылок в месяц. На входе — грязные использованные бутылки, на выходе — чистое сырье для производства новых.
Сбор сырья производится по сортировочным станциям и полигонам бытовых отходов.
Часть сырья поступает из сотни специальных контейнеров для бутылок, установленных заводом в Солнечногорске, но это — капля в море.
В России не привыкли к тому, что мусор может стоит денег, да и раздельный его сбор не развит (доля «разделки» у завода — не более 1%). Часть бутылок завод закупает у фитнес-клубов и отелей, но и это погоды не делает. Главный источник сырья — обычные свалки со всей страны (везут даже с Урала), где мусор сортируют вручную, выделяют из него бутылки, после чего пакуют и продают заводу. 300-килограммовые кипы грязных прессованных бутылок привозят на территорию завода, где они ждут своего часа.
Первый цех занят отбором и сортировкой бутылок. Все оборудование предприятия европейское, от лидеров отрасли переработки ТБО — BRT Recycling Technologie GmbH (Германия), TOMRA Systems ASA (Германия), RTT Steinert GmbH (Германия), BOA (Голландия), SOREMA (Италия), BUHLER AG (Швейцария).
Кипы загружаются в бункеры сортировочных линий, после чего происходит их распаковка и сортировка.
По большому счету, завод мог бы работать автоматически, но в российских реалиях это невозможно. Автоматические линии умеют различать и раскладывать бутылки по цветам, но как в Европе, где пластик поступает в переработку в чистом виде, у нас это не работает — в связи с очень сильной загрязненностью исходного сырья необходима помощь человека, и не одного.
Несколько бригад рабочих вручную сортируют бутылки, срезают этикетки, выкидывают затесавшийся мусор и тару, которая не может быть переработана — например, целиком затянутую в термоусадочный пластик, с посторонними предметами внутри или нестандартного цвета. Для переработки подходят только голубые, коричневые, бесцветные и зеленые бутылки. Последние, к слову, пользуются наименьшей популярностью у заказчиков.
Отсортированные по цветам бутылки вновь прессуются в кипы, и перевозятся на улицу — на склад, где ожидают попадания во второй цех.
В следующем цеху все начинается с распаковки «отсортированных» кип,
после чего бутылки отправляются на мойку.
Здесь тара «стирается» сначала в холодной воде, потом в горячей, потом в щелочном растворе и специальном моющем средстве.
Бутылка отмывается снаружи, растворяется клей, которым была приклеена этикетка. После серии моек — очередной пост ручной сортировки и магнитная металлосепарация.
Следующий этап — дробление. Бутылки измельчаются вместе с пробками, после чего получившиеся хлопья снова проходят процедуру тщательной очистки. В специальном барабане, заполненном жидкостью, происходит отделение бутылочного пластика от пробочного. Плотность у них разная, и хлопья от пробок всплывают на поверхность.
Бутылочные хлопья проходят процедуру финальной индуктивной металлосепрации, после чего специальный компьютерный станок отбирает бракованные флексы другого цвета.
Затем часть продукции упаковывают в 2-метровые мягкие контейнеры, так называемые Big-Bag. Флекс — прекрасное сырье для изготовления различных хозтоваров, стройматериалов и даже… флисовой ткани!
Перед запуском в дальнейшее производство, берется проба полученных хлопьев, которая отправляется в химическую лабораторию для различных тестов.
После этого хлопья пневмотанспортом подаются в третий цех — на линии экструзии и гранулирования. Процесс полностью автоматизирован.
Процесс в третьем цеху состоит из нескольких этапов. Во первых, повторное металлоотделение, потом предварительный разогрев, удаление ацетальдегида и других вредных примесей, фильтрация.Сначала хлопья режутся в измельчителе, после чего флекс плавится при температуре 280 градусов Цельсия.
Специальная машина — фильера выдавливает из расплавленного и очищенного пластика тонкие нити (стренги), которые осушаются и режутся на гранулы.
Аморфный гранулят транспортируется на кристаллизацию и далее поступает в реактор.
После 16-ти часовой поликонденсации в реакторе, под воздействием азота и высокой температуры аморфный гранулят превращается в финальное сырье — высоковязкий ПЭТ-гранулят для производства ПЭТ-бутылок.
Каждая партия продукции повторно контролируется — полученные гранулы внимательно изучаются специалистами.
Готовый продукт упаковывают в большие мешки, после чего отправляют заказчикам.
Гранулят одобрен для использования в упаковке для пищевых продуктов согласно экспертному заключению ФБУЗ «Центр гигиены и эпидемиологии Московской области». Бутылки из него получаются точно такие же прозрачные и чистые, как и из обычного гранулята, полученного химическим путем. Именно поэтому одним из клиентов завода является компания Coca-Cola.
В год завод, на котором работает 150 человек, может выпускать до 10 тысяч тонн готовой продукции, но текущий объем меньше. Причина — нехватка исходного сырья… Именно поэтому одним из организаторов туров на завод «Пларус» является организация… GreenPeace. Экологи приветствуют раздельный сбор мусора и переработку пластика — этот процесс в три раза меньше вредит планете, чем обычное производство пластика.
Серьезный повод задуматься!
Оригинал поста
kak-eto-sdelano.livejournal.com
Зачем школьники собирают пластиковые бутылки — Новости Петербурга
Обмен на саженцы
Как объясняют инициаторы проекта, сбор пластик может всерьез потеснить сбор макулатуры. За собранные пластиковые бутылки старательный сборщик получает саженцы липы, лиственницы, голубой ели и кедра.
«Тому, кто хочет получить лиственницу, надо сдать пять килограммов бутылок, за голубую ель придется собрать девять. Пластик сдается в переработку, а деньги, вырученные за него, идут на приобретение саженцев», — объясняет организатор движения «Круг жизни» Максим Вережинский. Он напоминает, что пластиковый мусор наносит природе непоправимый вред.
1 кг пластика — это 37 пол-литровых бутылок; 29 — литровых, 26 — на 1,5 литра; 11 — 5-литровых.
«Многие понимают это, и Петербург — не первый российский регион, присоединившийся к проекту. Надеемся, что этот эксперимент получит еще большее распространение, приживется в России», — говорит Вережинский и в числе плюсов называет снижение нагрузки на городские свалки, оздоровление воздуха и «антимусорное» воспитание детей.
Сбор пластиковой тары — хлопотное и трудоемкое дело. Как и макулатуру, дети приносят ее из дома, от родных, друзей и соседей.
Мусор и выживаемость
По мнению председателя Северо-Западного отделения общественной экологической организации «Зеленый крест» Юрия Шевчука, сбор макулатуры, скорее, «вчерашний день», а пластиковых бутылок — дело, с точки зрения экологии, полезное.
На одного петербургского и областного жителя ежедневно приходится примерно килограмм бытовых отходов (в числе прочего мусора — те же бутылки). Гражданин нашей страны в среднем производит за жизнь около 25 тонн мусора.
«Пластиковые бутылки легкие, но по объему могут занимать до трети пухто. Соответственно, мусоровозы вынуждены вывозить содержащие воздух бутылки, что нерентабельно. Чем меньше бутылок и банок окажется там, тем лучше. Поэтому, на мой взгляд, есть смысл в централизованном сборе, — объясняет он. — Вполне разумно рассказывать детям о проблемах утилизации и перспективах переработки мусора.
Вторая часть проекта вызывает вопросы. Я бы предостерег тех, кто не искушен в таком деле, как посадка полученных за сданный пластик саженцев липы, лиственницы и, тем более, голубой ели, от самостоятельных действий. Это требует особых знаний. Рекомендую довериться профессионалам, иначе выживаемость деревьев окажется слишком низкой, и труды пропадут даром».
Напоминает эксперт и о том, что в нашей стране во вторичную переработку сегодня идет не больше 10% твердых бытовых отходов, а прием пластиковых бутылок и металлических банок организован только в десятке больших городов.
Приведи в порядок планету
В то время как дети собирают пластиковую тару, взрослому населению России предложено подумать о возвращении практики массовой сдачи стеклотары. Во всяком случае, в депутатской среде это обсуждалось, как ранее сообщал ОК-информ.
Основной аргумент аналогичен: существенно сократится площадь свалок, а следовательно, меньше ущерба будет нанесено окружающей среде. Депутат парламента Ленобласти Владимир Петров в письме премьер-министру Дмитрию Медведеву объяснял, что в нашей стране люди ежегодно выбрасывают 1,2 млн тонн стеклотары и примерно столько же — пластика. «А мы ведь можем уменьшить площадь свалок — на десятки и сотни гектаров», — горячо убеждал парламентарий.
«Истина, как всегда, на поверхности, — считает человек, много лет занимающийся защитой природоохранных территорий, эколог Алексей Травин. — Боюсь показаться банальным, но главное — не сокращать титаническими усилиями площадь свалок, а просто стараться не безобразничать, не разбрасывать мусор».
Фото из архива Максима Вережинского.
ok-inform.ru